
オフセット印刷でのトラブル
1.裏移り
現象 |
印刷物が積み重ねられた状態で、印刷物の表面または裏面のインキが反対面について
汚れとなる。2色以上が重なった部分で多く発生。 |
原因 |
用紙の吸い込みが悪い、用紙の平滑性が良い、インキの盛りが多い、デリバリー部の調整が不適切、スプレーパウダーの種類と散布量が不適切、積み重ね枚数が多いなど。 |
対策 |
スプレーパウダーの散布量を増やす、高濃度インキでかすり気味に印刷する、裏付防
止剤(弊社ホストン等)を添加して印刷する、デリバリー部の吸引車・ファンを調整する、ドライヤー量を増やす、用紙の積み重ね枚数を減らすなど。 |
2.紙むけ
現象 |
紙がブランケットから離れる瞬間に紙の繊維やコート層がむけること。 |
原因 |
紙の表面強度が弱い、インキのタックが高い、印圧が強いなど。 |
対策 |
弊社DコンパウンドあるいはNテックスを添加してインキのタックを下げる、印圧を
軽めにする、用紙を別ロットに替えるなど。 |
3.つぼ上がり
現象 |
印刷機のインキつぼからインキが正常に呼び出しローラーに移らなくなり、印刷物の
インキが薄くなっていくこと。 |
原因 |
インキの流動性の不足。 |
対策 |
ワニスなどを添加してインキを柔らかくする、インキつぼローラーの回転数を上げる
など。 |
4.地汚れ
現象 |
版面の非画線部が感脂化(油となじみやすくなる)してインキがつき、印刷物が汚れて
くる。プレートクリーナーで拭いても、簡単には汚れが取れない。 |
原因 |
水上げ量が少ない、湿し水の整面効果が弱い、インキの乳化量が水上げ量に対して不
適切、製版時の非画線部の処理が不充分、機械の調整不良など。 |
対策 |
水上げ量を増やすかインキ供給量を減らす、エッチ液の添加量を多くし温度を下げる
(10℃以下)、用紙のpHが4以下又は8以上であれば用紙を取り替えるなど。 |
5.浮き汚れ
現象 |
インキが湿し水の表面に浮遊して、版面の非画線部に淡色の細かな汚れが発生する。
この汚れは、版そのものの汚れではないので、版面を拭けば汚れは取れるが、汚れ位置が移動するので浮き汚れといわれる。 |
原因 |
インキが柔らかすぎる、湿し水の調整が不適切など。 |
対策 |
タックの高いインキに替える、湿し水を絞る、エッチ液の濃度を適正に調整するなど。 |
6.トラッピング不良
現象 |
多色機による印刷で、先刷りインキの上に後刷りインキがつきにくい。 |
原因 |
タックバランス不良(後刷りインキのタックが高い)、インキの濃度バランスが不適切、
図柄、水上げ量が不適切(多い)、機械調整不良など。 |
対策 |
後刷りインキのタックを下げる、先刷りを高濃度インキでかすり気味に刷るなど。 |
7.モットリング(梨地)
現象 |
印刷面のシャドー部(濃色部)のインキの着きが不均一で、濃淡のムラができる。 |
原因 |
インキが柔らかすぎる、インキの盛りすぎ、印圧が強すぎ、用紙のムラなど。 |
対策 |
コンパウンド、ワニス、溶剤などでインキ粘度を調整する、高濃度インキでかすり気
味に刷る、印圧を軽めにするなど。 |
8.パイリング
現象 |
ブランケット、版、ローラーなどの上にインキがたまり、画線太り、印刷濃度の低下
などの原因となる。 |
原因 |
版の場合 インキがさくすぎる、インキ中に粗い粒子がある、乳化によりインキがさくくなるなどが原因となる。
ブランケットの場合 タックが高すぎる、用紙の表面強度が弱い、紙紛が多い、先刷りパウダーが多すぎるなどが原因となる。 |
対策 |
版の場合 高粘度ワニスなどを加える、湿し水を出来るだけ絞るなど。
ブランケットの場合 レジューサーなどでインキのタック・粘度を下げるなど。 |
9.ゴースト
現象 |
印刷方向に対して、面付け、図柄の影響で、印刷面上に濃淡が現れる。 |
原因 |
図柄の配置、インキが硬く流動性が悪い、インキが濃すぎ盛りが少ない、インキ着け
ローラーの調整不良など。 |
対策 |
ワニスを加えてインキの流動性を上げる、低濃度のインキで盛り気味に刷る、インキ
着けローラーのセッティングを調整するなど。 |
10.ヒッキー
現象 |
印刷物に部分的にドーナツ状の白抜けが発生する。 |
原因 |
インキの乾燥皮膜、紙紛、あるいは風により飛来したホコリなど。 |
対策 |
缶からインキを出すとき乾燥皮膜が入らないようにする、インキ使用量の少ないユニ
ットのインキつぼ両端は乾燥しやすいため時々撹拌する、空調の風向きを変えるなど。 |
11.転移不良
現象 |
インキの紙へのつきが悪く、所定の印刷効果が得られない。 |
原因 |
インキの粘着力の不足、インキのしまり、インキのタック、被印刷体など。 |
対策 |
高粘度ワニスなどを加える、インキの乾燥が速過ぎるときは乾燥抑制剤を加える、弊
社DコンパウンドあるいはNテックスを添加してタックバランスを整えるなど。 |
12.画線太り(ドットゲイン)
現象 |
画線や網点が太くなって、画線の白抜き部分が埋まり気味となる。 |
原因 |
インキが柔らかすぎる、濃度が低い、タックが低い、印圧が高い、水上げ量が多すぎる、湿し水のpHが高いなど。 |
対策 |
インキが柔らかすぎる場合は弊社マジックハードを添加して硬めに調整する、印圧、
水上げ量などを調整する。 |
13.乾燥不良
現象 |
印刷物が長時間経過しても乾燥しない。 |
原因 |
紙のpHが低すぎる、紙の通気性が悪い、湿し水のpHが低すぎる、印刷物保管場所
の温度が低すぎる、湿度が高すぎる、インキの乾燥が遅すぎるなど。 |
対策 |
インキにドライヤーを入れる、湿し水のpHを調整する、通風を良くする、印刷物保
管場所の温度を上げるなど。 |
14.カール
現象 |
印刷直後に紙が反る。 |
原因 |
用紙の目、インキのタックが高い、紙の表面繊維が湿し水で伸縮する、図柄など。 |
対策 |
縦目用紙の場合は横目の用紙に変更する、インキのタックを下げる、湿し水をなるべく絞る、印圧を軽めにするなど。 |
15.耐摩擦性不良
現象 |
印刷物同士が擦れて印刷面に傷が入ったり、包装紙のインキが手や衣服と擦れて汚れ
たりする。 |
原因 |
インキのワックス量が少ない、マットインキ、用紙の表面状態、用紙の吸油性、不完
全な乾燥での後加工など。 |
対策 |
用途によりいろいろな問題がありますのでインキメーカーに御相談下さい。 |
16.ブロッキング
現象 |
1次ブロッキング インキが乾燥する過程でインキの粘着性のために印刷物が互いに接着する。
2次ブロッキング 完全乾燥後の保管印刷物が互いに接着する。 |
原因 |
1次ブロッキング インキの盛りが多すぎる、積み上げ時の温度・湿度が高い、積み上げ
時の加重の掛けすぎ、インキの乾燥が遅い、用紙の平滑性がよいなど。
2次ブロッキング インキの盛りが多すぎる、積み上げ時の温度・湿度が高い、積み上げ
時の加重の掛けすぎなど。特に多湿時に発生しやすい。 |
対策 |
1次ブロッキング 高濃度インキで出来るだけかすり気味に刷る、裏付防止剤(弊社ホス
トン等)を添加して印刷する、ドライヤーを添加し乾燥しやすい環境
にする、積み上げ枚数を減らすなど。
2次ブロッキング 高濃度インキで出来るだけかすり気味に刷る、保管は風通しの良い場
所で高温を避ける、積み上げ枚数を減らすなど。 |
17.ローラーストリッピング
現象 |
「ローラーはげ」とも言われ、印刷機の金属ローラーやゴムローラーにインキが付着
せず、はげたようになる。 |
原因 |
金属ローラーの不感脂化、湿し水のpH・量・成分などが原因となる。 |
対策 |
金属ローラーを整面液処理する、湿し水の濃度を適正値に合わせ、水を絞るなど。 |
|
 |
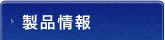
|